Mastering Metal Cutting: A Symphony of Selection, Precision, and Productivity
5 min read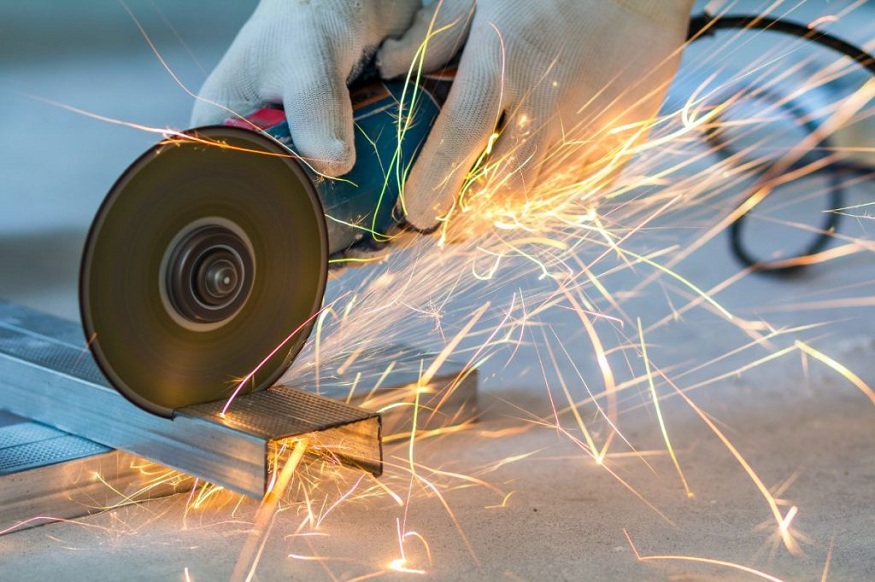
A typical supermarket has 35 different bean cans and 48,750 SKUs. Now consider that even in inch sizes, major cutting tool manufacturers each carry over 40,000 SKUs (exactly like the bean cans)! By sheer statistics, choosing the best can of beans is far easier than selecting the greatest cutting tool! Choosing tools that suit the machine and cut the component features at the best quality, fastest cycle time, and lowest cost is known as tool selection. We will go over a few of the major factors to consider when choosing a metal cutter tool here.
The Most Vital Instrument
Production ceases if even a single tool breaks down. That being said, not every instrument needs the same level of care. When everything else is equal, the tool with the longest cut time will have the most impact on cycle time, thus you should pay the most attention to it. Pay close attention to the tool with the closest tolerance that cuts important parts characteristics. Furthermore, greater consideration should be given to instruments like drilling, grooving, and threading that are most likely to provide subpar chips. Downtime is caused by bad chips.
Suitable for the Device.
Because different tools are best held with different hands, it’s important to know which one to use. To get a general idea of which tools work with which spindles, right-handed tools are often compatible with CCW machines while left-handed tools are compatible with CW machines. If your lathe collection includes models that can be turned with either the right or left hand, it’s best to stick with tools that are designed for left-handed users. Tools used by mills tend to be excessively flexible. Although extended-reach tools may reach more components, they are not without their drawbacks. Stiffness is lost rapidly, tool deflection increases, cutting rates drop, and chatter is more likely.
Tool Dimensions
Choosing an excessively big mill and an excessively tiny lathe tool is a typical error. While bigger milling tools cost more and take longer to cut air, larger lathe tools are more robust. Larger instruments often have higher costs than smaller ones.
Regrindable as Opposed to Indexable
It’s easy this one: stay away from grinding tools. When given the option, you should choose an insertable or indexable design, with the rare exception of certain drills and end mills. You’ll get more consistent outcomes and reduce labor expenditures.
Grades and Tool Material
A number of variables come into play here, including the material you’re cutting, the machine’s feed limits, and its speed. If you’re picking a material class, go with the coated grade as it’s the most versatile. Make use of the manufacturer-supplied grade selection charts. A common mistake is trying to solve a tool life problem using a brand grade cross reference chart. Choosing the most similar brand won’t likely improve your outcomes if the one you have isn’t functioning. Observe the manner of failure carefully.
Power Needs
Use what you paid for is the driving concept in this case. When parts and fixtures permit, you should use tools and cutting data that utilize 80% of the power available if you purchased a 20-hp mill. The machine owner’s manual’s power/rpm charts should be carefully examined. Choose cutting tools that are optimized for cutting inside the machine’s power band’s efficient zone.
The Count of Edges
The maxim “the more, the better” applies here. Typically, the cost of a lathe tool with twice as many cutting edges is not doubled. The number of cutting edges per insert has increased over the last ten years due to advancements in the design of cutoff and grooving inserts as well as certain milling inserts. It is not unusual to swap out an outdated milling cutter with four cutting edges with a contemporary one with up to sixteen cutting edges. Productivity and feedrate at the table are directly impacted by the quantity of healthy teeth.
Comparing Modular Construction to One-Piece Design
Larger tools are more suited for modular designs, whereas small tools work best with one-piece designs. In the event of a major tool failure, you want the smaller, less costly component to be involved. This is particularly true for boring and grooving tools.
Single-Use as Opposed to Multipurpose
Generally speaking, a multipurpose tool is better ideal for smaller parts. One multipurpose tool that can drill, turn, bore, thread, and chamfer, for instance. Multi-function tools work well with more complicated components. When the tool is in the cut, not when it’s being indexed, is when a machine generates revenue.
Regular or Unique
When CNC was first introduced, the general consensus was that specials were obsolete since the form of the component was now determined by the software rather than the tool. However, only 15% of cutting instruments used in large quantities now are unique. Why? precise measurements, a decrease in station, and time savings. Take into account the contribution of a specialized instrument to cycle time reduction if your lot size is significant. The cost and lead time between standards and specials are becoming shorter because to developments in bespoke on-demand manufacturing.
Coding
The toolpath has to be defined once you have a CNC machine, a component, and a tool. Ideally, you know how to use an advanced CAM product and have a good grasp of machine code. Tool characteristics (e.g., ramp angles, directions of cut, feed, and speed) must be taken into account by the toolpath. Programming approaches exist to decrease cutting force, enhance chips, and minimize cycle times for any kind of metalworking tool. An excellent CAM program may significantly reduce labour costs and increase output.
Cost
While price is significant, the cost of the tool is much more significant. The tool’s price is what you pay for it. The actual cost of a tool depends on how productive it is. Often, the lowest priced tool is the most expensive one. The cost of the cutting tool, as a proportion of the part’s total cost, is only 3 percent. Pay more attention to a tool’s productivity than its initial cost.
In summary
Achieving accurate and economical metal machining requires careful selection of the appropriate metal cutting equipment from the trusted metal cutting tool suppliers in saudi arabia. Purchasers of metal-cutting tools may optimize production processes, increase productivity, and save costs by being well-informed about the various kinds, materials, coatings, geometries, and other considerations to take into account. Metal cutting tools are significant assets in any machining environment and may be further ensured to last a long time and work continuously with proper care and storage.